Wheels and tires
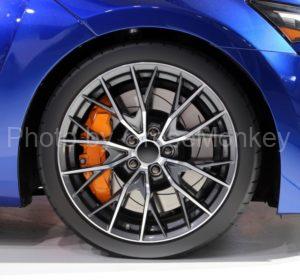
The wheels hold the tires in contact with the road surface, transmit the driving force, braking force and steering function to the tires, and function to make the vehicle run smoothly.
The tires, together with the wheels, support the load of the vehicle, absorb the impact from the road surface, transmit the driving force and braking force to the road surface, and function to make the vehicle run smoothly.
Wheels and tires greatly affect the functions of each device such as suspension, brakes, and steering of automobiles.
table of contents
Wheel structure and function
The wheels have the strength to withstand the load of the car, the impact from the road surface, the centrifugal force when turning, the heat dissipation to dissipate the heat of the tires and brakes, the driving force and braking force, and the followability of the suspension. Weight reduction to improve and roundness to prevent wheel vibration are required.
Strength
Various forces are acting on the wheel, and this force is called “stress”, and there are stress received when the car is stopped, stress during running, and stress remaining on the wheel itself.
What is stress(Japanese): https://katuhito.site/en/stress_strain/
The stress received when the vehicle is stopped is a stress consisting of the load of the vehicle, the stress tightened by the hub bolts and nuts, the air pressure of the tire and the repulsive force of the bead portion of the tire due to the air pressure.
In other words, the wheel needs to be strong enough to withstand various stresses.
Heat dissipation
Since the wheels must dissipate the heat generated by the tires and brakes, the shape has been devised to improve heat dissipation.
Aluminum wheels are almost certainly superior in heat dissipation compared to steel wheels. Good heat dissipation reduces the possibility of brake fading and vapor lock.
Problems due to heat dissipation occur when the brakes are used a lot on long downhill slopes. Under such circumstances, the heat conductivity and heat dissipation of the well-ventilated aluminum wheel exert its function in direct contact with the brake disc or brake drum.
Weight saving
The mass of the wheel is included in the unsprung load along with the suspension arms, axles and tires. Therefore, the smaller the unsprung load, the better the followability to the movement of the suspension, and the quick absorption of the generated vibration improves the riding comfort and motility.
In general, in these performances, it is said that a weight reduction of 1 kg of unsprung load is comparable to a weight reduction of 20 kg of unsprung load.
Characteristics by material
Generally, iron and a light alloy are used as the material of the wheel, and the light alloy includes an aluminum alloy and a magnesium alloy.
Wheels made of steel plate are called steel wheels, aluminum alloys are called aluminum wheels, and magnesium alloys are called magnesium wheels.
The metal specific density is 1.7 for magnesium, 2.7 for aluminum, and 7.9 for steel, with magnesium being the lightest. (The standard of specific gravity is water, about 1.0 g / cm3 at 4 ° C)
When viewed from the material itself, steel is harder and stronger than light alloy in the order of steel, aluminum, and magnesium.
Aluminum is a lightweight metal with excellent thermal conductivity, castability, machinability, etc., and is advantageous in terms of weight reduction and high accuracy, but its corrosion resistance is lower than that of steel, so paint it. It is supplemented by giving.
Types and characteristics of light alloy wheels
Aluminum wheels help reduce unsprung load, and aluminum wheels are used not only in passenger cars but also in some large vehicles.
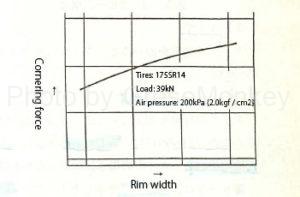
Figure 1: Rim width and cornering force
Figure 1 shows the cornering force for the rim width. In terms of mass, aluminum wheels can take a relatively large rim width compared to steel wheels, and the increase in rim width increases the cornering force. It is connected to.
Cornering force: => link
Magnesium wheels are lighter than aluminum wheels and have excellent dimensional stability and impact resistance, so they are used only for applications that require light weight and high strength, but they are inferior in corrosion resistance and free design. ..
Magnesium wheels: https://en.wikipedia.org/wiki/Alloy_wheel#Magnesium_alloy_wheels
Aluminum alloy wheel structure

Figure 2: 1-piece structure
Figure 2 shows the one-piece casting of the rim and disc of the wheel, which allows precise dimensional finishing but increases the actual weight.

Figure 3: Two-piece structure
Figure 3 shows a cast or forged disc on a squeezed or stamped rim that is welded or bolted together. It is lightweight and has excellent design freedom of the disc part.

Figure 4: 3-piece structure
Figure 4 shows the design of the disc part, which is obtained by dividing the rim part that has been squeezed or pressed into two parts (front side rim and back side rim), welding it to a cast or forged disc, and then tightening bolts to strengthen it. And has excellent versatility
Tire structure and function
When a load is applied to a tire, the tire exhibits various characteristics depending on the state at that time, and the main ones will be explained.
Tire deflection
As the load is applied to the tire, the tire causes “deflection”. For this “deflection”. There are three types of deflection, vertical deflection, width deflection, and horizontal deflection, which are indispensable elements for the function of tires.

Figure 5-1: Vertical deflection
Figure 5-1 shows the vertical deflection. The vertical deflection that occurs when a load is applied vertically gives an appropriate installation area and softens the impact from the road surface, but when the limit is exceeded, It causes tire fatigue and wear.

Figure 5-2: Width deflection
Figure 5-2 shows the width deflection, which occurs at the same time as the vertical deflection when a vertical load is applied. In this case, it is the deflection that occurs in the left and right width directions.
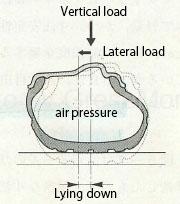
Figure 5-3: Horizontal deflection
Figure 5-3 shows the lateral deflection, which is the lateral deflection that occurs when a longitudinal load is applied and then a lateral load is applied.
In addition, the JIS standard defines the load corresponding to the tire pressure and its upper limit, and when a load is applied, the tire radius in the stationary state and the running state is defined as follows. ..
Attach the tire to the applicable rim and fill with the specified air pressure. The shortest distance from the center of the tire axis to the tread when placed perpendicular to the flat plate in a stationary state and a specified load is applied.
It is the value obtained by dividing the mileage per rotation of the tire by 2π when the tire is mounted on the automobile using the applicable rim, the specified air pressure and load are applied, and the tire is run at a constant speed (60km / h).
- Dynamic load radius specified in JIS
For passenger car tires, fill with air pressure for the design working load (see note). The value of the radius when traveling on a flat and straight dry road surface at a constant speed of 60 km / h with a normal design load applied is used as a reference.
For tires other than passenger car tires, refer to the radius value when running at a constant speed of 60 km / h with the maximum load applied at the maximum air pressure (single wheel when there is a distinction between single wheel and double wheel). I have to.
The speedometer of an automobile displays the speed and the mileage based on the radius of dynamic load and the rotation speed of the tire.
The dynamic load radius is slightly larger than the static load radius due to the influence of centrifugal force during traveling. (Dynamic load radius> Static load radius)
(Note): The maximum recommended load that can be applied to the tires with spare tires and tools and the specified number of passengers added to the specified positions when the vehicle is empty.
Tire buffering action
The impact from the road surface is directly absorbed by the tire, and further absorbed by the shock absorber, chassis spring, or the like.
The buffering action of a tire depends on the shape, dimensions, material, structure, etc. of the tire, but is also greatly affected by the air pressure and load.
When the tire pressure is constant, the amount of tire deflection changes approximately in proportion to the load applied to the tire. From this, the tire is considered to be a kind of spring.
The static vertical load required to give the tire a vertical deflection of 1 mm is called the static vertical spring constant, and the smaller this value, the easier it is to absorb the impact received from the road surface, and the ride quality improves.
Tire rolling resistance
- Resistance due to tire road surface and friction
Since the tire slips at the contact part with the road surface, resistance due to friction occurs. This resistance is generally about 5 to 10% of the rolling resistance of the tire, but the road surface condition and the tire structure, etc. It is affected by the tread pattern and so on.
- Resistance due to tire deformation
Each time the tire rotates, it is compressed by the road surface and repeatedly returns to its original shape.
If the rubber or tire cord that makes up the tire is a completely elastic body, the energy required for compression is completely released when it returns to its original shape, but in reality, the energy released as elasticity is only a part. This is the cause of resistance due to tire deformation. This resistance is the largest of the rolling resistance of the tire.
The rolling resistance of a tire is affected by road surface conditions, speed and tire type, structure, air pressure, and the like.
Tire heat generation
The tire is periodically deformed due to contact with the road surface during traveling, and a part of the energy is converted into heat by this bending / stretching action.
Further, since the material of the tire is not a good conductor of heat, the generated heat is accumulated inside the tire and the temperature of the tire rises.
If the internal temperature of the tire rises abnormally, the strength of the rubber and the tire cord and the adhesive strength of the tire components will decrease, causing separation (peeling) and bursting.
This heat generation varies depending on the tire pressure, load, speed, running time, tread groove depth, carcass structure, and the like.
As the traveling time and traveling speed of the automobile increase, the number of bending and stretching movements of the tire increases, and the degree of heat generation increases. Along with this, the heat generated by the tire is accumulated inside and at the same time partly dissipated to the outside, so after a certain period of time, it settles at a constant temperature as shown in Fig. 5-4.
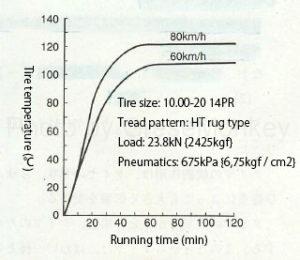
Figure 5-4: Running time and tire temperature rise
Tire vibration
Tires inevitably have some manufacturing imbalances such as force (rigidity) and mass (weight) that do not change shape with respect to dimensions and external force, and these cause vibration.
Generally, uniformity (balance) in a broad sense that includes all of rigidity, dimensions, mass, etc. is called uniformity .
- Vibration due to non-uniform dimensions
If the radius of the tire is different in each part, the tire will vibrate when it rotates. (Runout: Rotating body shake and lateral shake are generally called runout)
Even if the tire itself does not have a dimensional deviation, runout may occur due to improper assembly of the tire and rim. In addition, there is vibration in both the tire and the rim, which may overlap and appear as vibration larger than the touch of the tire itself. In such a case, perform ” phase alignment” by slightly shifting the positions of the tire and rim and refitting.
- Vibration due to non-uniform rigidity
The tire rotates while acting like a spring while being flexed under a load. However, due to the partial difference in the thickness of dust and the seams of the carcass, there is an imbalance in rigidity, and subtle changes occur in the deflection of each part on the tire circumference, which impacts during high-speed rotation. It becomes a force and appears as a vibration of the tire.
Vibration due to unbalanced tire weight
If one part of the tire is heavier than the other part, I think it will rotate slowly and the part will stop at the bottom. The unbalance at this time is called static unbalance, and during the rotation of the tire, an extra centrifugal force acts on this part, causing the tire to vibrate up and down.
If the tire does not have a static imbalance, the tire may run out when rotated at high speeds. The unbalance at this time is called dynamic unbalance, and it mainly causes shimmy .
The automatic vibration caused by kickback due to unevenness of the road surface mainly transmits the vibration around the kingpin axis to the steering wheel, which makes the driver’s hand uncomfortable. The generated vehicle speed is in a very wide range, and its frequency changes in proportion to the vehicle speed.
Tire running noise
The running noise of a tire is generally smaller in a rib type pattern than in a lug type pattern, and is smaller in a radial tire than in a bias tire. Tire running noise is mainly classified into the following three types.
The sound produced when the air in the groove of the tire tread pattern is compressed between the road surface and the tire and discharged, producing a sound with the same frequency as the number of times the pattern pitch passes per second.
It is a sharp “key” sound that occurs when starting suddenly, braking suddenly, turning suddenly, etc., and is generated when the tread of the tire causes local vibration with respect to the road surface.
- Sound due to unevenness of the road
It is the sound of air intake and exhaust when the tires pass through the unevenness of the road, and when the road surface is specially processed, it becomes a sound like pattern noise.
Tire life
The main factors that affect the life of a tire are heat generation, impact, fatigue, wear, etc., and the degree of these varies greatly depending on the air pressure, load, speed, temperature, road surface condition, driving method, and the like.
Of these, the air pressure and load are particularly important, and using them at the specified air pressure and load is the first condition for extending the life of the tire.
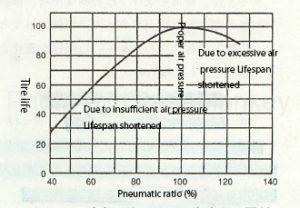
Figure 5-5: Relationship between air pressure and tire life
Figure 5-5 shows the relationship between air pressure and life. The proper air pressure is 100%, and the vertical axis shows the tire life with the proper air pressure at 100%.
When a load is applied to a stationary tire, the ground contact portion bends. In a running tire, this deflection is repeated to generate heat, and the temperature of the tire rises.
As the speed increases, the number of deflections per unit time increases, so the amount of heat generated also increases, which adversely affects the rubber that is the main component of the tire and shortens its life.
Further, when the air temperature or the road surface temperature is high, the heat dissipation of the tire becomes poor, so that the temperature of the tire rises and the life is further shortened.
Tire flatness ratio
If the flatness ratio of the tire is reduced, the riding comfort is slightly deteriorated, but the turning performance, the maneuvering performance at high speed, the driving performance and the braking performance are improved.
This is because the cornering force is increased and the road holding during running is stabilized by increasing the contact area and the lateral rigidity of the tire.
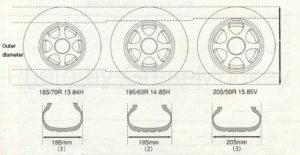
Figure 5-6: Tire flatness ratio
By rearranging the size of the tire and the wheel without changing the outer diameter of the tire itself as shown in Fig. 5-6 in the same model of automobile, we devised so that the tire with the flatness ratio suitable for the purpose of use can be selected. Has been done. By the way, the reason why the ride quality deteriorates is that the smaller the flatness ratio of the tire, the better the grip force of the road surface, but the smaller the amount of deflection of the tire, the less the vibration can be absorbed.